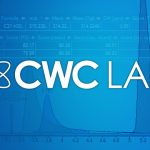
Monday, February 15, 2016 by healthrangerinventions
http://www.healthrangerinventions.com/2016-02-15-german-test-facility-gears-up-for-larger-turbines-long-blades.html
As the size of offshore wind turbines has grown, so has the need for new facilities at which to test them. New facilities are now in operation in Denmark and in the UK, adding to well known facilities such as those at NREL in the US. The dynamic nacelle testing laboratory at Fraunhofer IWES may not be the most powerful of these facilities, but scientists there believe it unique in its ability to test nacelles, drivetrains and components mechanically and electrically and do so at the same time. Opened in October 2015, the DyNaLab will be complemented from 2018 by another facility designed to make blade testing more realistic.
(Article www.owjonline.com, republished from http://www.owjonline.com/news/view,german-test-facility-gears-up-for-larger-turbines-long-blades_41846.htm)
“Although described as a nacelle testing laboratory, the DyNaLab is much more than that,” said Professor Jan Wenske, deputy director of Fraunhofer IWES. “We can use it to test nacelles, drivetrains, main bearings and a range of components. All test rigs differ, but in the DyNaLab, we have an especially high level of functionality. Unlike some other rigs, we also offer an extremely high level of grid emulation as well as all of the mechanical testing one would expect from a facility like this. The combination of the two – the high-level mechanical testing and the grid/electrical emulation – is what distinguishes this facility.”
Among Fraunhofer IWES’s first customers at the DyNaLab are Adwen, which is using the facility for long-term tests on its new 8MW turbine. Professor Wenske said the tests would make full use of advanced functionality that the facility can offer and would see Fraunhofer IWES test the entire drivetrain in the 8MW unit and components within it and conduct endurance testing of the turbine. A ‘virtual’ 36,000V medium voltage grid integrated into the 10MW rig enables short circuits and other faults in a grid to be tested with a high degree of accuracy and repeatability. The duration of testing can be adapted to a certifier’s specific requirements, and real-time models and control algorithms can be used to simulate real-world loads and interactions between the nacelle and rotor. “With the grid and the hardware-in-the-loop load simulations, a range of loading scenarios can be simulated in a reproducible manner,” he explained. “The performance of a turbine can be tested in the event of an emergency stop or multiple dips in the grid following storms or short circuits due to faulty pitch regulation. By simulating operational conditions with extreme loads, companies such as Adwen can accelerate the verification process. The process will allow individual and fully integrated subsystems to be validated as well as complete drivetrain operation at full power.”
Florian Sayer, head of department, structural components division at Fraunhofer IWES, explained the company has a successful history of testing turbine blades but wanted to upgrade its facilities in order to be able to test ever-larger turbine, longer units. Testing a 40m blade might take Fraunhofer IWES three to four months, but testing an 80m blade or blades that are longer still had become a more time-consuming process. Phase 1 of the new blade testing facility, which is being funded to the tune of €10 million by the Federal Ministry for Economic Affairs and Energy and the Federal State of Bremen, is due to get underway in mid-2018. Phase 2 of the work at the new facility should be underway by the end of 2018. Apart from enabling Fraunhofer IWES to test blades more quickly, speeding development of new technology and reducing costs, the new facility will also enable the testing organisation to undertake testing that is much more representative of real-world loading. It will also enable Fraunhofer IWES to undertake root segment and blade tip tests separately. This will mean that tests can be undertaken at higher frequencies and with a more accurate load profile. Individual sections with critically high loads and parts of the blade with greater material thickness or strong curvature can also be investigated separately. This approach should produce more detailed results and reduce testing times by around 30 per cent.
Read more at: http://www.owjonline.com/news/view,german-test-facility-gears-up-for-larger-turbines-long-blades_41846.htm
Tagged Under: Tags: Nacelle Labs, Testing laboratories, Wind Turbines